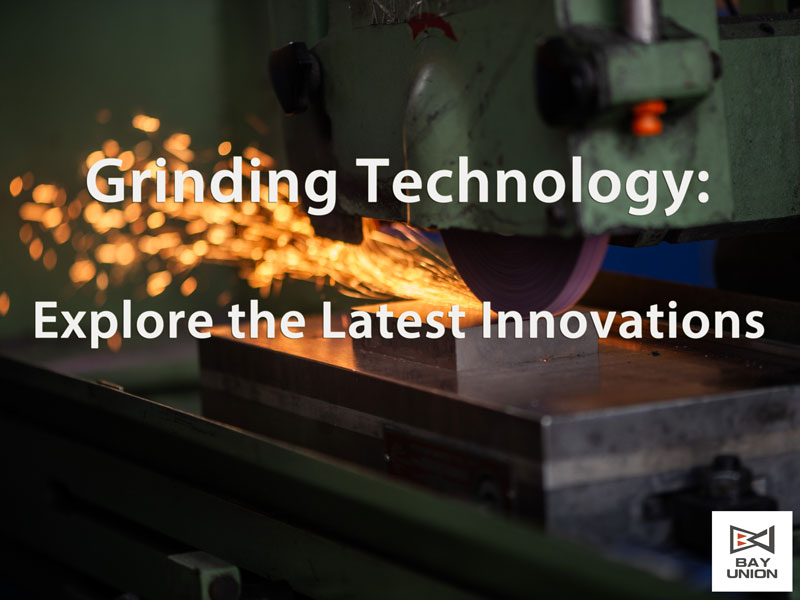
Grinding Technology: Explore the Latest Innovations
Introduction
Are you looking to enhance your manufacturing processes with cutting-edge grinding technology? At Bay Union Abrasive Technology Co., Ltd., we stand at the forefront of innovation, crafting grinding solutions that cater to the dynamic needs of various industries. Our dedication to advancing grinding technology ensures that our clients are equipped with the most efficient, precise, and robust tools available, driving their success in an ever-evolving marketplace.
Advances in Grinding Techniques
Ultra-Precision Grinding: This method achieves extraordinarily tight tolerances, crucial for industries where precision is paramount, such as aerospace and medical device manufacturing. Ultra-precision grinding allows for the creation of components with surface finishes and dimensional accuracies that are measured in nanometers, enhancing the performance and longevity of critical parts.
Cryogenic Grinding: By using low temperatures to make materials brittle, cryogenic grinding improves their breakability, which is particularly beneficial for processing tough, thermally sensitive polymers and organic materials. This technique preserves the quality of the material by preventing heat-induced degradation, making it ideal for pharmaceuticals and food products where maintaining chemical stability is essential.
High-Speed Grinding: This technique involves higher feed rates and cutting speeds, which significantly reduce grinding time and increase productivity. High-speed grinding is effective for large-scale manufacturing processes, where reducing cycle time is critical. It also helps in maintaining the thermal integrity of the workpiece, preventing surface burns and ensuring the metallurgical properties are not altered.
The Role of Smart Technologies
Smart technologies are profoundly transforming grinding operations. Machines equipped with real-time feedback systems adjust parameters instantly based on detected changes in material conditions or tool wear, ensuring consistent quality. Adaptive control systems dynamically modify operating conditions to optimize grinding performance. Internet of Things (IoT) connectivity facilitates the remote monitoring and management of equipment, leading to proactive maintenance, reduced downtime, and streamlined production workflows, greatly improving the overall reliability and efficiency of grinding operations.
Material Innovations
Innovations in abrasive materials continue to propel the industry forward. The introduction of novel synthetic materials and improvements in the thermal properties of abrasives allow for more efficient material removal and longer tool life. These developments significantly reduce the ecological footprint of grinding operations by minimizing waste and energy consumption.
Benefits of Advanced Grinding Technology
The advantages of cutting-edge grinding technologies are significant:
- ▶ Increased Efficiency: Modern automated grinding technologies significantly cut down on operation times, boosting production rates dramatically. Automation allows for continuous operation without the need for frequent manual adjustments, leading to a more streamlined production process that can operate 24/7 with minimal human intervention.
- ▶ Enhanced Precision: Advanced grinding machines are equipped with precision controls and fine measurement systems, ensuring components are produced within extremely tight tolerances. This precision is crucial for applications in industries like aerospace and microelectronics, where even the slightest deviation can result in the failure of an entire system.
- ▶ Improved Surface Integrity: The use of sophisticated grinding techniques and better abrasive materials leads to improvements in the surface finishes of components. This not only enhances the aesthetic and functional qualities of the parts but also significantly extends their lifespan by reducing wear and tear. Superior surface integrity is especially important in applications such as bearing surfaces and optical components, where smoothness is critical.
Environmental Impact and Sustainability
As global environmental concerns rise, the grinding industry is also shifting towards sustainable practices. Innovations such as recycling used abrasives and developing less toxic bonding materials are making grinding technology more environmentally friendly. These changes not only help companies comply with regulations but also appeal to a growing base of eco-conscious consumers.
Future Trends and Predictions
Looking to the future, we anticipate even greater integration of automation and data analytics into grinding technology. This will likely include advanced predictive maintenance, machine learning algorithms for process optimization, and further developments in eco-friendly technologies. These innovations will continue to transform grinding processes, making them more efficient, accurate, and sustainable.
Conclusion
At Bay Union, we continue to invest in research and development to push the boundaries of grinding technology. Our aim is to provide our customers with grinding solutions that not only meet but exceed their expectations in terms of performance, precision, and reliability. Explore our latest innovations and see how they can transform your manufacturing processes.
For more insights and to keep up with the latest developments, please connect with our team of experts. We are here to support your business with cutting-edge solutions that lead the way in the abrasive technology industry.