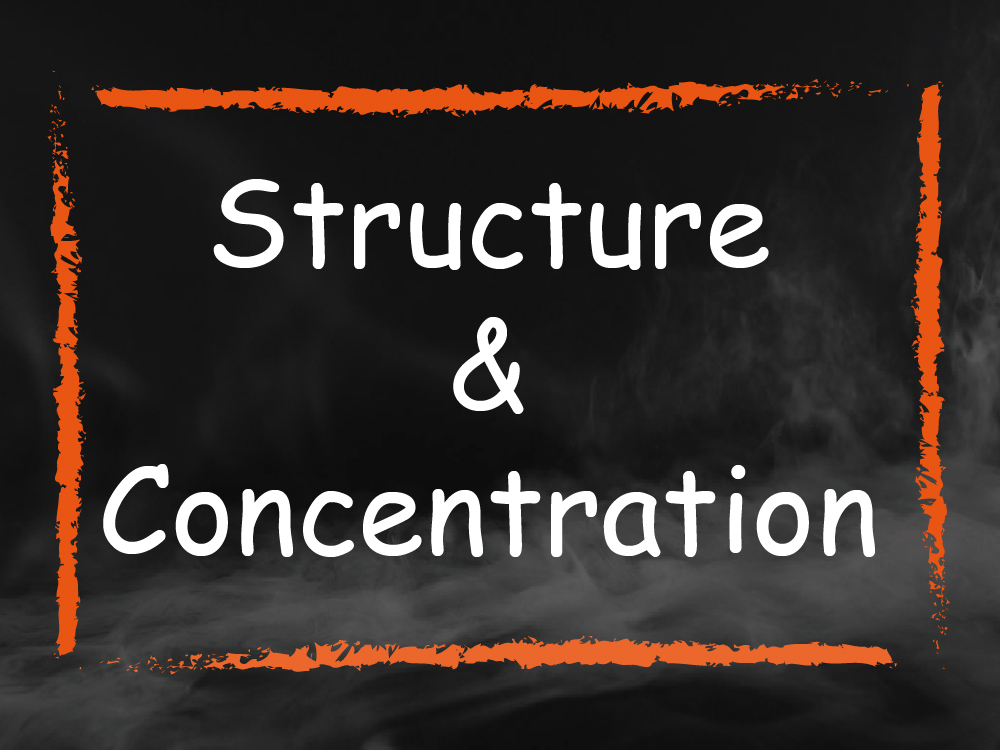
Structure & Concentration
The structure uses a number to indicate the proportion of abrasive material in a grinding wheel, known as the abrasive ratio. A rating of 6 signifies a 50% abrasive ratio, with each lower number increasing the ratio by 2%, and each higher number decreasing it by 2%. Consequently, a rating of 5 represents a 52% abrasive ratio, while a rating of 7 represents a 48% abrasive ratio. To aid in memory, one can associate the organization's number with the average distance between abrasives, where a higher number indicates a greater distance, equivalent to a lower proportion of abrasive material in the grinding wheel.
Natural Pore Structure |
||||||||||
Structure | 1 | 2 | 3 | 4 | 5 | 6 | 7 | 8 | 9 | 10 |
Abrasive Rate | 60% | 58% | 56% | 54% | 52% | 50% | 48% | 46% | 44% | 42% |
Furthermore, we can divide the structure into two ranges: 1-10 and 11-20. In the 1-10 range, the grinding wheel can naturally form pores, and the distance between the abrasive particles is sufficient to support the structure of the wheel. However, in the 11-20 range, due to the abrasive particles being too far apart, it is necessary to add an artificial pore-forming agent during the mixing of the grinding wheel raw materials. This agent helps to compensate for the loose structure within the wheel, aiding in wheel formation, and after sintering, it becomes a porous grinding wheel.
Porous(Porosity) Structure | ||||||||||
Structure | 11 | 12 | 13 | 14 | 15 | 16 | 17 | 18 | 19 | 20 |
Abrasive Rate | 40% | 38% | 36% | 34% | 32% | 30% | 28% | 26% | 24% | 22% |
Generally, a porous grinding wheel can provide better self-sharpening, efficient cool grinding, easy removal of metal chips, and lower grinding forces. On the contrary, due to a lower proportion of abrasive particles in the wheel, it can be challenging to remove the grinding residue completely, especially when grinding larger areas, requiring additional feed rates. Additionally, a lower abrasive ratio can lead to a decline in grinding cutting force when the grinding wheel size decreases. Therefore, it is essential to choose the appropriate organization for different grinding applications to achieve a good balance.
For superabrasive grinding wheels, which use higher-priced materials like CBN (cubic boron nitride) or diamond, the abrasive ratio is expressed in terms of concentration. Typically, concentrations are marked in multiples of 25 as a grading scale. A concentration of 25 means that within one cubic centimeter of volume, there is 1.1 carats (0.22 grams) of abrasive material. Similarly, a concentration of 50 indicates the presence of 2.2 carats of abrasive material, and so on. The highest commonly seen concentration is 200, which corresponds to 8.8 carats per cubic centimeter.
Concentration | Carat | Gram | Abrasive Rate |
25 | 1.1 | 0.22 | 6.25 |
50 | 2.2 | 0.44 | 12.5 |
75 | 3.3 | 0.66 | 18.75 |
100 | 4.4 | 0.88 | 25 |
125 | 5.5 | 1.1 | 31.25 |
150 | 6.6 | 1.32 | 37.5 |
175 | 7.7 | 1.54 | 43.7 |
200 | 8.8 | 1.76 | 50 |
By matching grinding wheels with different structures, it can be likened to using saw blades with varying tooth counts. From a theoretical standpoint, this corresponds to different intervals between cutting edges. Using an open-structured grinding wheel with larger intervals between cutting edges provides better cutting ability but may lead to a rougher workpiece surface. To overcome this, the grinding wheel's rotational speed can be increased, and careful selection of a suitable diamond dressing tool is necessary to achieve both excellent cutting performance and the desired surface roughness.